Management of production in ERP software
- May 21, 2018
- 4 min read
Updated: Oct 22, 2018
Today we will discuss how to do management of production in ERP software.

This topic is useful for production business such as textile, furniture industry, Handloom industry, food processing industry, plastic industry etc.
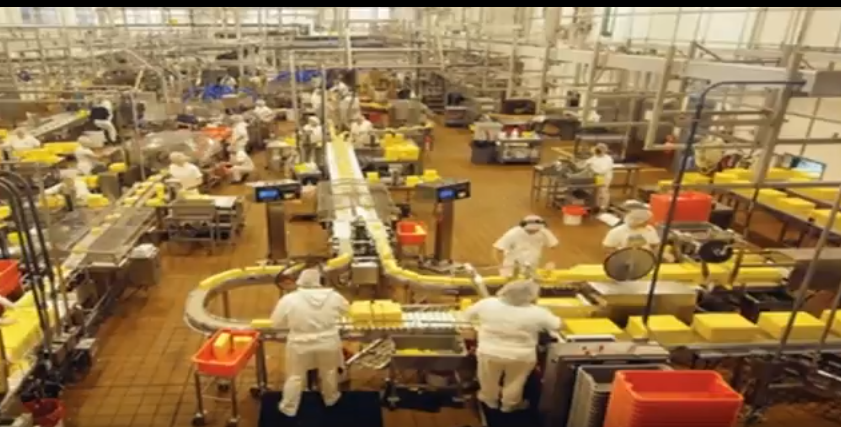
It includes all production in which raw material converted to finished goods. ERP software is very flexible for all type of business.
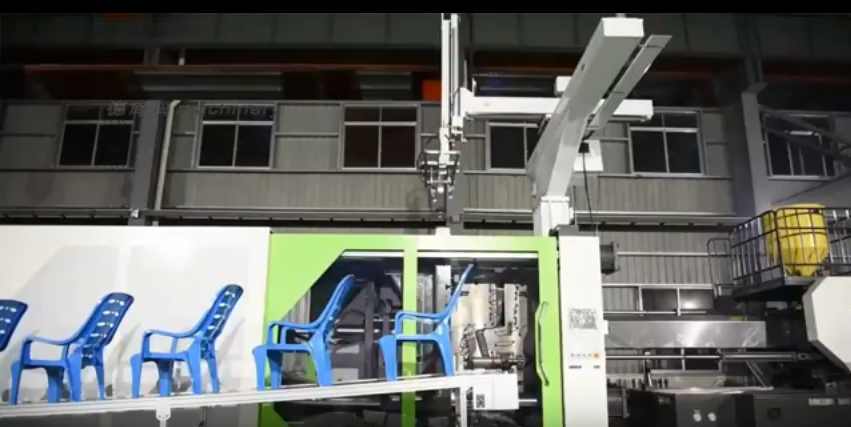
If you know how much raw material required and how much by product produce from a finished product then you have to define process firstly. If you have not any knowledge of it then you can manage the production without process.
LET US START

First of all click on feature/Nature of business in utilities menu.

Tick on production. Click on update. Now close it.
Now let us take example of plastic industry. Here we will manage the production of plastic products.
Firstly we will create all finished item and raw material of our business.
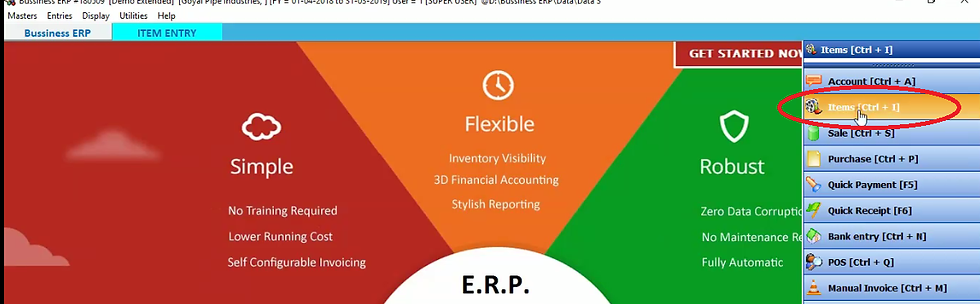
Click on item on right hand side.

Click on new.

Now fill finished item name in item name block. For eg. We are taking plastic chair in item name. Select tax slab, company and group. As we select plastic chair as item thus we select pieces as primary unit for a chair. Now fill sale price per plastic chair. Now click on save.

Now we will create raw material for plastic chair as an item. Click on new.

Suppose plasic dana is required for a plastic chair as a raw material then we will fill plastic dana in item name. Select tax slab, company and group. Select Kg in primary unit as plastic dana is available in Kg. Suppose we have 500 kg plastic dana. Then we will fill this value in opening stock. Now click on save.
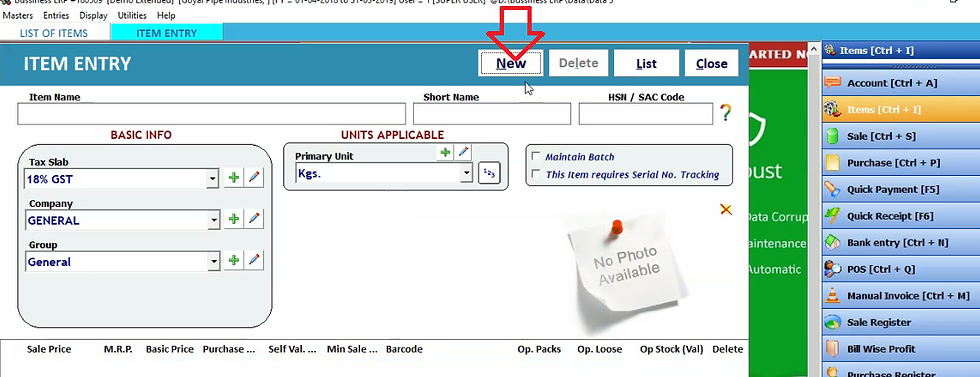
We will create colour(raw material) as an item. Click on new.

Now fill item name, tax slab, company and group. Now select gms as primary unit. Fill opening pack with the grams of colour available with us. Click on save.
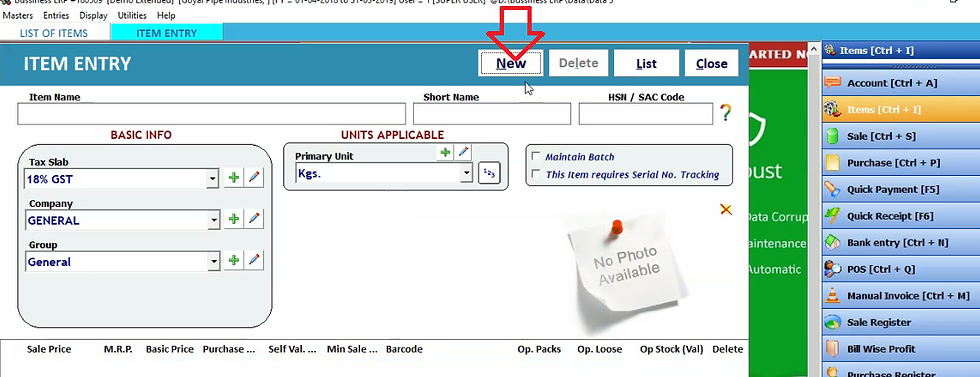
The remaining of plastic after finishing of plastic chair known as scrap. We will create scrap as an item. Thus click on new.
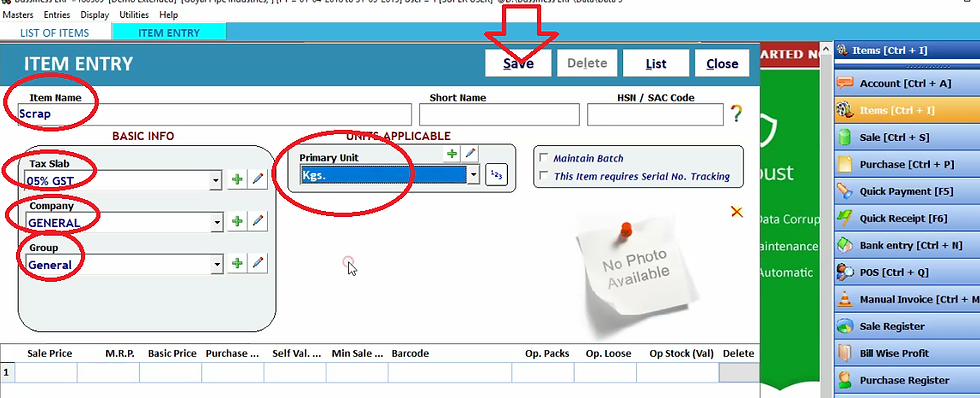
Now fill scrap as item name. Select tax slab, company, and group. Now select primary unit and click on save. Now close it.
Now we will do process entry.

Click on process in master menu.
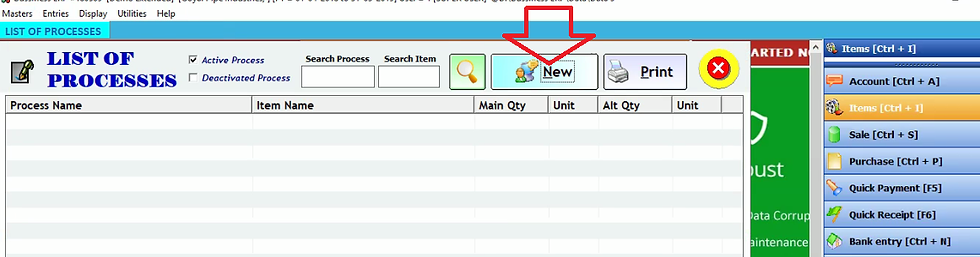
To create a new process click on new.

Now we will fill the details of raw material required for a process. Now fill process name as chair manufacturing. Now select main item after process thus we will select here plastic chair. Now fill quantity. For eg. We take 1 in quantity, it means to manufacture one chair how much raw material required we will fill details next. Select the raw material required and the quantity of that raw material required to manufacture one plastic chair. Now click on add item.

Now select another item and fill the quantity and click on add item.

Now we will select bye product produced after manufacturing of one chair. Suppose after manufacturing of one chair 500 kg scrap/bye product generate then we will select 500 in quantity. Now click on add item.
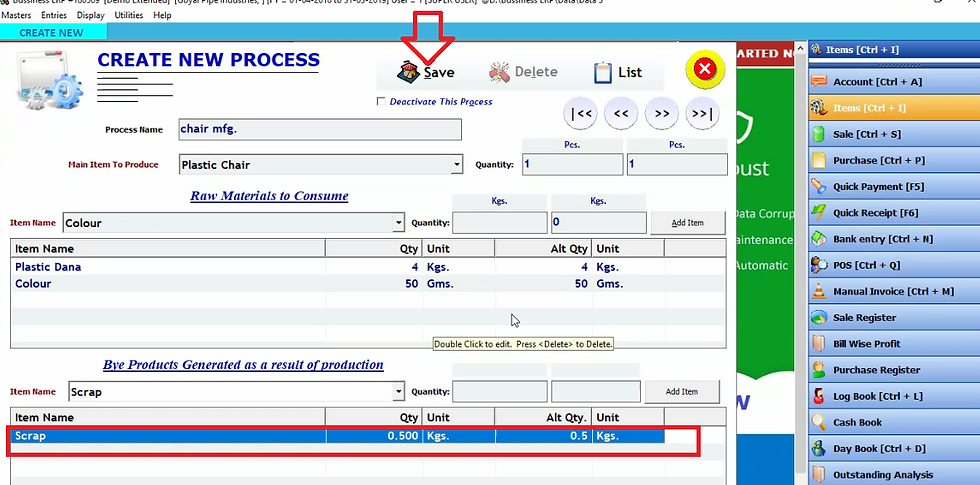
Now click on save. Close it by clicking on close button.

We will do production entry. Click on production in entries menu.

To generate a new entry click on new.

Now fill date and voucher number. Select process for production entry. Now the software will automatically select the main item to produce. Suppose we have done 50 chair production then we select 50 in quantity and click OK.

After clicking OK software will automatically display the scrap generated and raw material used for 50 chair. Now click on save and close it.

Now we will check stock report by clicking on stock report in display menu.
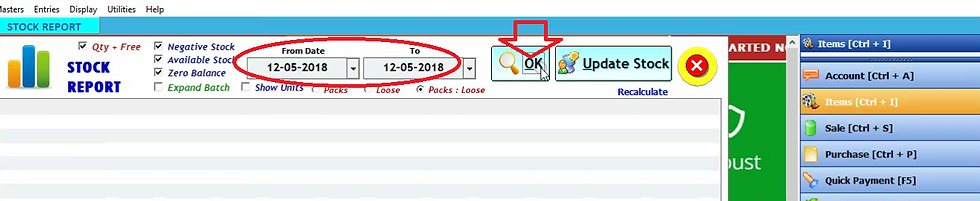
After selecting date range click OK.

Thus it display the stock of all items such as finished tems,raw material and scrap. Now close it.
Let us suppose you have no idea of raw material required for the production of an item/finished goods. Thus in this case you need not to create process.

You can do it’s entry directly by clicking on stock journal in entries menu.
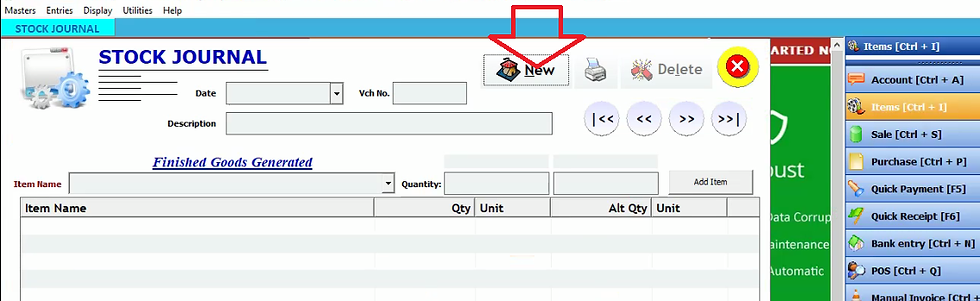
Click on new.

Now select finished good and quantity of finished good. Click on add item.

Now select raw material used to manufacture this item/finished good. Fill quantity of raw material required. Thus in this way you can fill the detail manually in case you have not prior idea of raw material to be used.

Now click on save. Now close it.
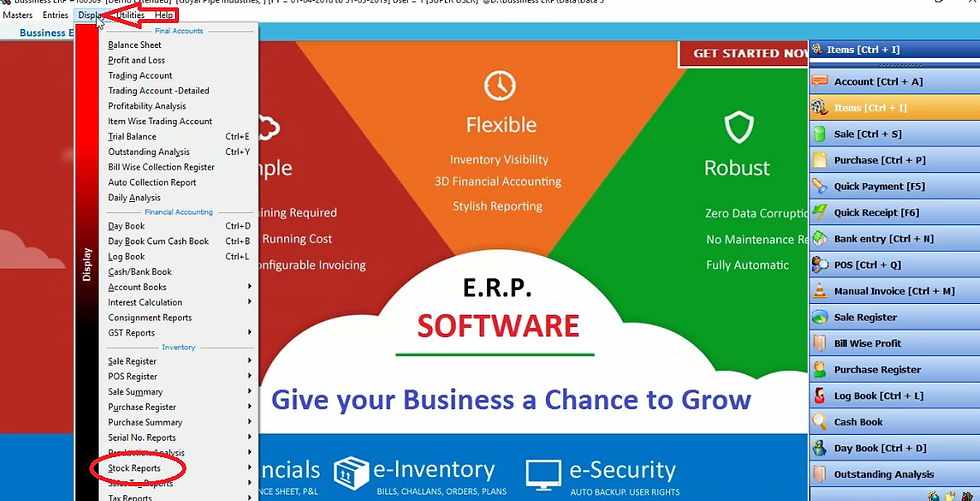
Now we will check stock report by clicking on stock report in display menu.

Select date range and click OK.

As we have done 30 chair entry in journal. Thus it display total 80 chair after adding 50 chair as created previously with 30 chair in journal entry. It also display the consumption of raw material and all other details. Now close it.
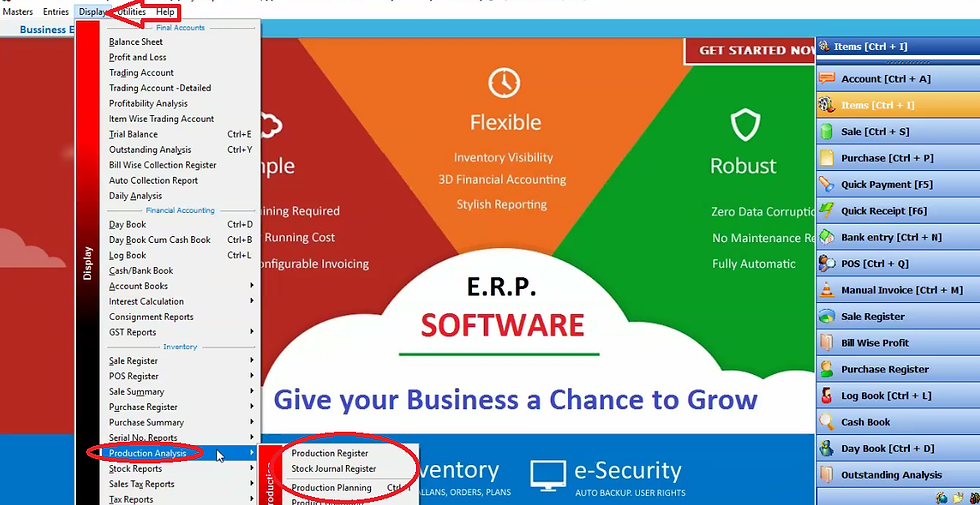
You can also check all production reports in production analysis in display menu.
If you want to check the quantity of raw material required for manufacturing of raw material.

Then click on production planning in production analysis in display menu.

Select the item to produce and process name. Click on add item.

After clicking on add item it will automatically shows the raw material quantity required to manufacture particular item. Now click OK.

Thus software will automatically display the quantity of raw material required to produce particular quantity of plastic chair.
Comments